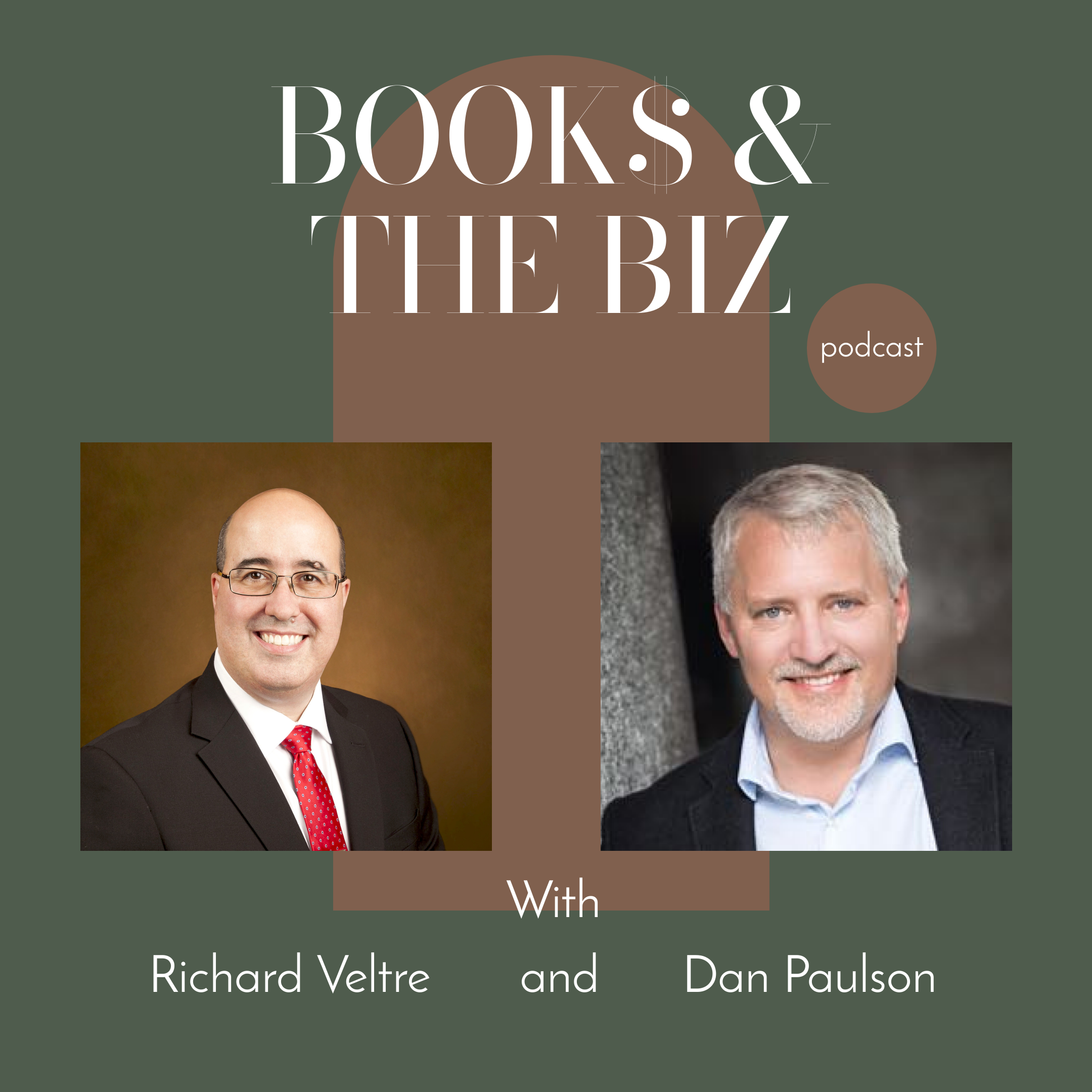
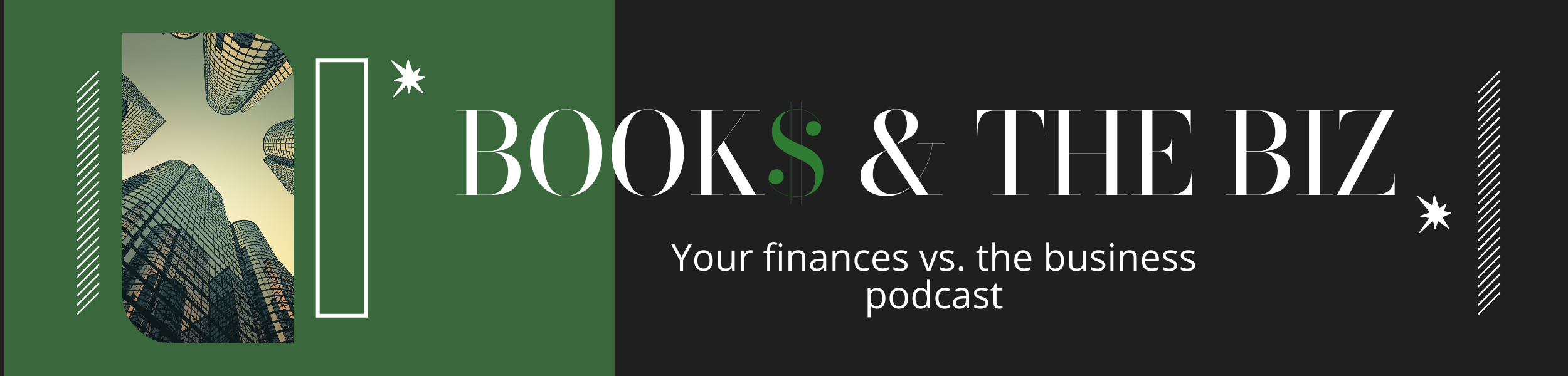
Tech Shortage! What It Takes to Recruit Right.
Books & The Biz
Dan Paulson and Richard Veltre | Rating 0 (0) (0) |
Launched: Feb 06, 2024 | |
dan@invisionbusinessdevelopment.com | Season: 2 Episode: 8 |
Part 2 of 4.
Our interview with Jay Goninen continues with what's happening in the Auto industry. It's much more than just hiring bodies. What matters is finding techs that are a good fit for the industry.
Jay Goninen is the Co-Founder & President of WrenchWay. Jay started working in his family's independent auto repair shop at the age of nine, and has worked in the industry ever since. Jay started his professional career as a technician, and then moved into management roles within the automotive and diesel industries. Jay is also the host of the Beyond the Wrench podcast.
SUBSCRIBE
Episode Chapters
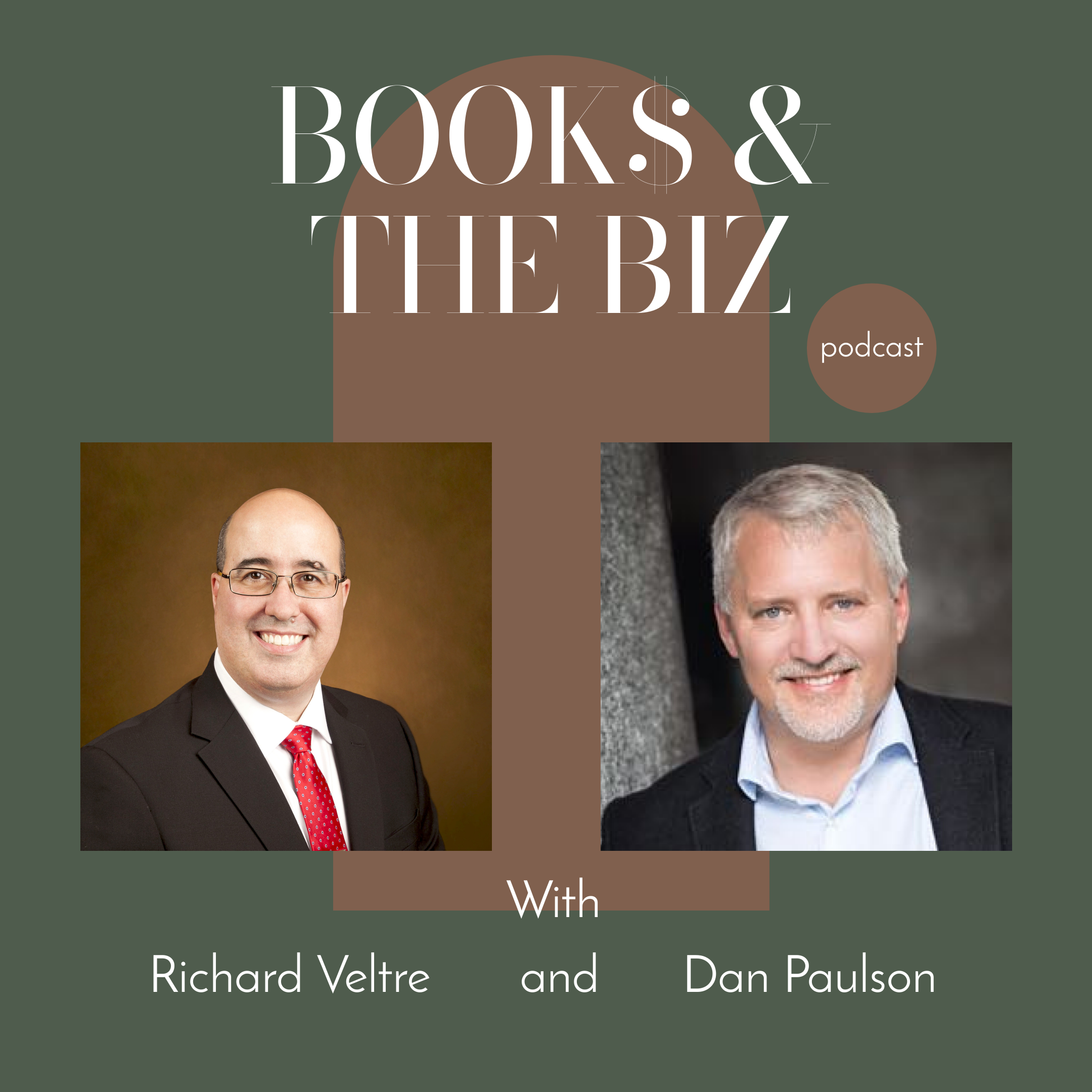
Part 2 of 4.
Our interview with Jay Goninen continues with what's happening in the Auto industry. It's much more than just hiring bodies. What matters is finding techs that are a good fit for the industry.
Jay Goninen is the Co-Founder & President of WrenchWay. Jay started working in his family's independent auto repair shop at the age of nine, and has worked in the industry ever since. Jay started his professional career as a technician, and then moved into management roles within the automotive and diesel industries. Jay is also the host of the Beyond the Wrench podcast.
[00:00:00.000] - Rich Veltre
Well, you piqued my interest on one thing, and that was that in your industry, because Dan and I have had a lot of conversations about motivation of people, et cetera. And so when you said that people are in the industry for two years and then they leave. And my industry, I can get that, right? Everybody wants to go work for the big firm, and then they find that training, and they get to launch, and they go into something else, or they go They go to a smaller shop and they bring the name and reputation of the bigger shop. So if in your industry, the people are leaving, my curiosity is, where are they going? I mean, if you're fixing, is it that they're getting the training from a bigger and going to a smaller, or are they actually leaving the industry? Because it sounded like they were leaving the industry.
[00:00:48.890] - Jay Goninen
Yeah, and I don't want to speak for every scenario, but in a lot of cases, they are flat out leaving the industry. Some get that baseline of technical knowledge like I did, and use that to parlay into different areas or different sectors of the same sector or different areas of the same sector. There are a lot of opportunities. I know I was just talking to somebody about this the other day, but when I was 20 years old or 25 years old, there wasn't a company like Wrenchway around, where we value some of that technical background, right? And there's more and more technical lines. There's more and more factory support types of roles than ever before. So I think there's just genuinely more opportunity. Now, the other side of I think there's a lot of kids that get into this and don't fully understand the industry. And I went to Universal Technical Institute in Chicago for school. And one of the real shames that I saw when I was there was that there were a lot of kids there that shouldn't have been there, right? They signed up because they saw the cool commercial and they wanted to attend.
[00:01:57.100] - Jay Goninen
Yet in reality, they shouldn't been there. And I think a lot of times the reason they get there is because they see what is perceived as the really sexy parts of the industry, which is working on cool cars and learning how to do cool things. But it's hard. It's really, really a hard job. And when that cool factor wears off and you're left with what your actual job is, I think a lot of people maybe start to understand at a little greater level that that's not for them. And that's where, with our work I've been a huge proponent of job shadows and apprenticeship type programs, because that kid can get exposure before they go spend tens of thousands of dollars in college, and another 10 grand right off the bat in tools to understand that they don't like it. It can put them in a really bad spot. And so I've had a lot of conversations with shops over the years, where I tell them that if you get a job shadow in, and they find out that that's not the career for them, or even an apprentice, an apprentice that comes in and works in the shop, you're doing that kid a gigantic favor, because you're going to save them a lot of money, a lot of heartache, and a lot of pain early on, that they don't need to have.
[00:03:15.840] - Jay Goninen
And likewise with the shop, they're not going to stick a bunch of money into a young person that's not going to stick around for a while, right? And I think with our industry, we're at such a lack of talent in the industry that It can be really appealing to hire that person that can fog a mirror and really comes in, and it doesn't matter what their skill level is. They can work on cars, and we just are desperate to get people to work on cars. So they do that out of desperation and out of more of a reactive approach rather than proactive. Well, where you can really solve a lot of problems is if you get serious with young people, and you're not just hiring that apprentice on just because they happen to show some interest in And then if you're in the industry, you actually have a pipeline of young people that go through a JobShadow program and understand what it's like to work there. You get a look at what that kid has to offer, and then if that makes sense, you bring them on to an apprenticeship type of opportunity. So rather than just bringing on anybody that shows interest, get more kids' visibility to what it is that we're doing, and then put them into that system.
[00:04:22.520] - Jay Goninen
And you'll save everybody a lot of time and heartache.
[00:04:28.050] - Dan Paulson
So what's the cost of onboarding a new technician now? Do you know it from the employer's side, what they tend to spend for that?
[00:04:38.090] - Jay Goninen
Yeah, it varies. And there's some where it's pretty much zero, because they don't do any onboarding. They throw them to the wolves. Yeah, yeah. So it varies drastically. And even I've seen mom and pops do it great and do it far better. There's one, we did a podcast with a A shop owner owns four shops in Minneapolis. He does the onboarding side better than anybody I've ever seen. He uses Trainual, if you're not familiar with Trainual, the software that you can put your policies and procedures in, but uses Trainual and really does just a very good job at the whole onboarding process. And on the opposite side of that, I've seen gigantic companies that absolutely suck at it, that just aren't good at onboarding at all. So I think it really depends on the size of the shop or dealership, maybe the focus that they put on it. I think it's really easy to shove it off on an HR person in a bigger company, and then hope that they're doing it the right way. But a lot of times, and I've gone through this experience myself, you spend time with the HR person, they do your first day paperwork that you need to get paid and get insurance and all that stuff.
[00:05:56.710] - Jay Goninen
And then they throw you the wolves, and then you just are just out in the shop, wandering around. You're not even sure where anybody is supposed to go or who you're supposed to talk to. And that is also one of the things, oftentimes in a shop, Mondays are the most chaotic day, and a lot of shops will start their people on a Monday, and it ends up with the first two or three hours of just sheer awkwardness. So it's really trying to really think through your process, and something as small as when they are actually starting can make a huge impact on that new employee satisfaction on coming to work for you.
[00:06:36.860] - Dan Paulson
Yeah, I definitely agree to that. How has the industry changed over the years? I mean, I think most of us, we have an image in our head of what a garage or what a dealership is like, and it's greasy, it's messy, it's oily, you're covered in grease up to your elbows. And while some of that's true, I think a lot of it's changed over the years, hasn't it?
[00:06:59.490] - Jay Goninen
I think it It's changed as much as when Henry Ford started getting things rolling off on an assembly line, right? It is far different than what we grew up with. And I grew up in a very greasy type of shop. I know dad always kept it. He took a lot of pride in keeping a clean shop, still does. But it was just a dirtier job back then. Now, there's still times where you're going to have oil and grease and the dirty parts of the job. But so much of the technology has taken over and will continue to take over, and to the point to where there's a shop in Madison called Precision Diagnostics. All they do is diagnostic work, and it looks like a laboratory in their shop. It is spotless. There is And there's no dust, there's no oil, there's no anything. In fact, part of their policy is they don't touch anything with oil. So they're a good client of ours at Rentsch way, but I think it's evolved so much, and to the typical consumer consumer, they really don't have an understanding of how complex these vehicles are now. And I think a lot of that, I fault our industry at not telling the story of that.
[00:08:11.690] - Jay Goninen
And I push a lot of shops to say, you should be talking to people because the price to get your vehicle fixed is starting to go up exponentially. And it's because you have to pay these qualified people. They're not working for 10 bucks an hour anymore, right? They're very, very well made professionals now. The tooling that goes into this stuff, you can't, that will forever begrudge a lot of the big parts chains because they make it sound like you can just pull up, we'll throw the scanner on, tell you what's wrong with your car, and you can buy that part and go get it fixed. And in reality, what happens is they hook it up at those parts houses. A lot of times that person, that might be the first time they've actually worked on something in their life. They plug in and it says O2 sensor. So they automatically replace the sensor. The customer gets really frustrated because it didn't actually fix their problem. Normally, there's something upstream of that sensor that's causing that sensor to go bad. And so that customer just paid 150 bucks for something that didn't fix their vehicle, that they're now going to have to go to an actual reputable shop to get diagnosed and repaired.
[00:09:25.370] - Jay Goninen
And so they're doubling up on costs that they don't need to. And maybe that O2 sensor was bad, but because something else caused it, you just ruined the new one, and you still haven't fixed the core of the problem. So I think when we look at how much this has changed, our industry has to do a better job at explaining the technology behind what it takes to repair your vehicle. On top of that, the liability is going through the roof right now. And some of you might be familiar with what they call a A-DAS. So a advanced driver assistance systems. I think I've got that acronym, right? But basically, that's all the cameras on your car. That's your lane keeping assistance. And in order to calibrate those sensors, You have to have a very specialized, very expensive machine. In that machine, if you don't do the proper calibration, or if you sign off that you did it, and that car gets in an accident, you're in trouble. And And so at a typical shop, when you have something as simple as your brakes replaced, or you have something else that might seem like a small thing, it's going to cost you an additional $300 to have that ADAS calibration done.
[00:10:48.540] - Jay Goninen
So the cost of repair is going to substantially go up as we move forward, and it's going to take a different professional level of service shop to be able to maintain the standards that are needed to even touch a car. And we're just at the start of the change. I mean, it's going to be a pretty crazy change over the next decade or so.