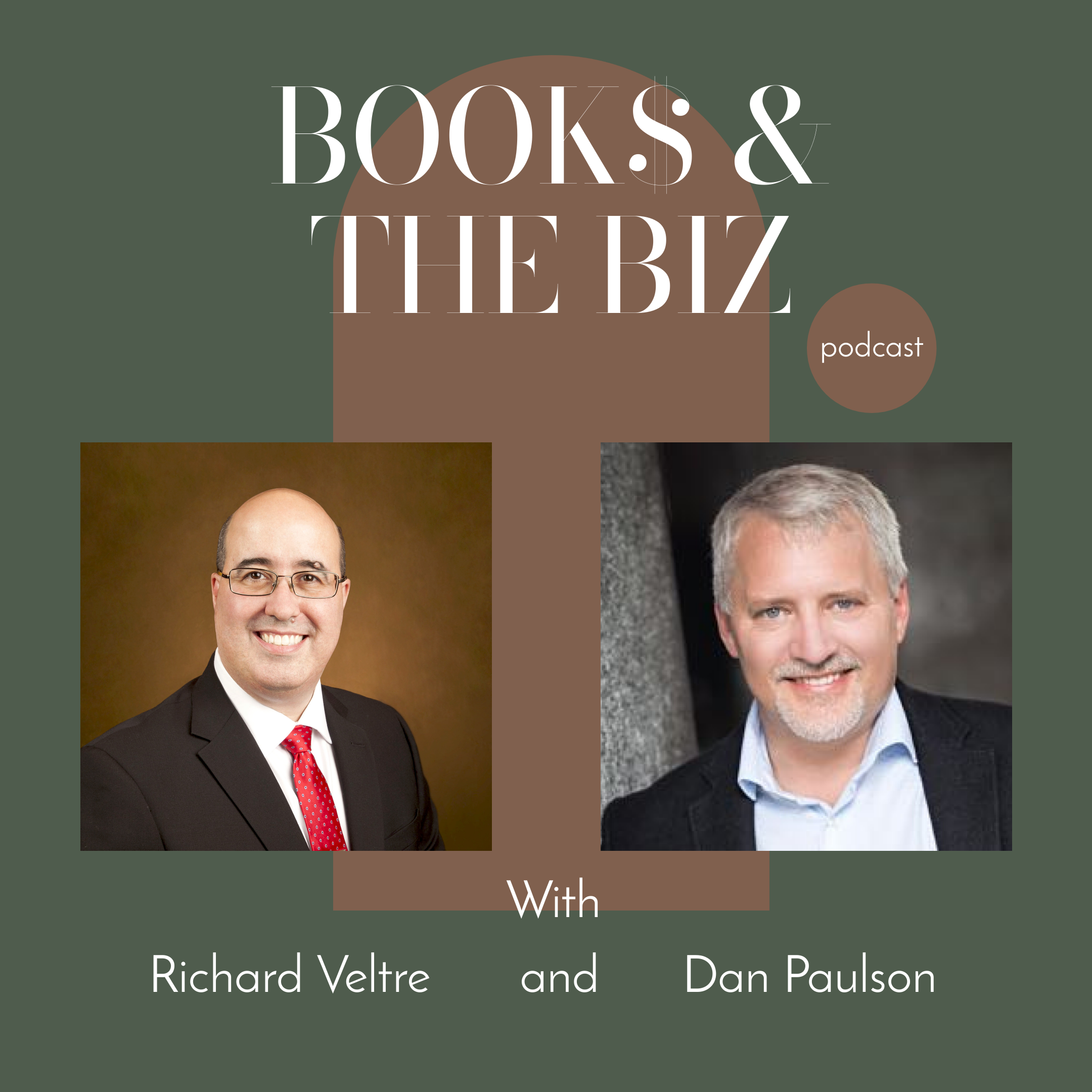
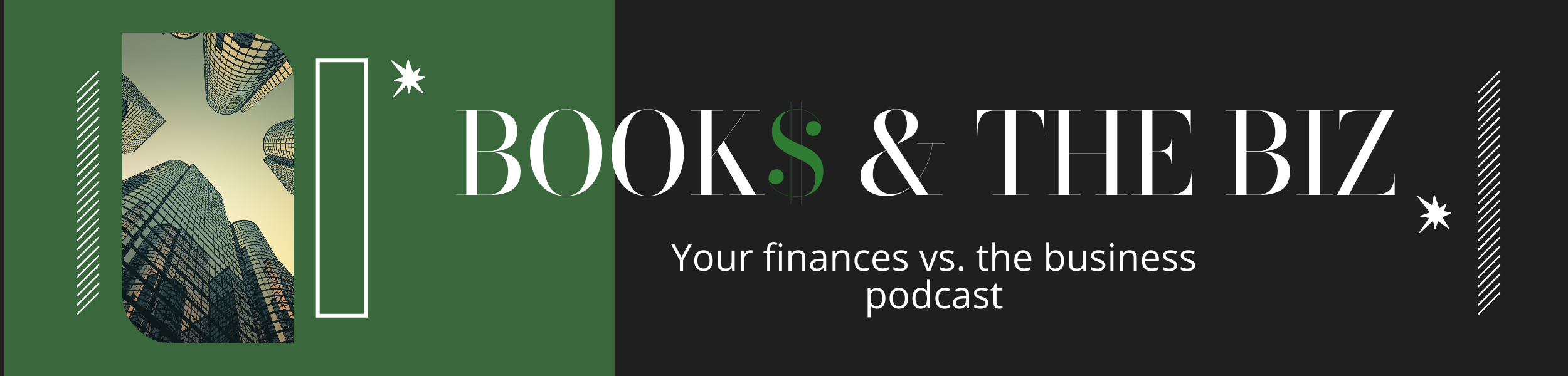
Will Robots Rule: The economics and politics of robotics in business
Books & The Biz
Dan Paulson and Richard Veltre | Rating 0 (0) (0) |
Launched: Jul 18, 2024 | |
dan@invisionbusinessdevelopment.com | Season: 2 Episode: 34 |
Will Robots Rule: The economics and politics of robotics in business
Books & The Biz
Published: Jul 18, 2024, Season: 2, Episode: 34
Artist: Dan Paulson and Richard Veltre
Episode Summary
Automation has become an essential tool for businesses looking to reduce costs and improve the quality of their products or services. However, there is a growing concern that this technology may also lead to the elimination of well-paying jobs for workers. In this episode of Books & The Biz, David Turner, Founder and President of Turner Business Solutions, will provide valuable insights into the impact of robotics on business operations.
Automation has become an essential tool for businesses looking to reduce costs and improve the quality of their products or services. However, there is a growing concern that this technology may also lead to the elimination of well-paying jobs for workers. In this episode of Books & The Biz, David Turner, Founder and President of Turner Business Solutions, will provide valuable insights into the impact of robotics on business operations.
Automation has become an essential tool for businesses looking to reduce costs and improve the quality of their products or services. However, there is a growing concern that this technology may also lead to the elimination of well-paying jobs for workers. In this episode of Books & The Biz, David Turner, Founder and President of Turner Business Solutions, will provide valuable insights into the impact of robotics on business operations.
Automation helps business lower costs and increase quality. Some argue it also eliminates good paying jobs for workers. This Books & The Biz episode talks with David Turner, Founder and President of Turner Business Solutions, who will share his insights on the impact of robotics on business, Why people implement automation and when businesses will start spending money on robotics again
[00:00:02.23] - Alice
Books in the Biz, a podcast that looks at both the financial and operational sides of success. Please welcome our hosts, Dan Paulson and Richard Veltre. Dan is the CEO of Envision Development International, and he works with leaders to increase sales and profits through great cultures with solid operations. Rich is CEO of the Veltre Group and a financial strategist working with companies to manage their money more effectively.
[00:00:30.06] - Dan Paulson
Now on to the podcast. Hello, and welcome to Books in the Biz. And speaking of automation, thank you, Alice. Alice is our lovely automated AI introduction there. But anyway, Let's talk further about automation. So today we have a guest with us. Richard, how are you doing, first of all?
[00:00:51.11] - Rich Veltre
I am doing very well, Dan. How about you?
[00:00:53.23] - Dan Paulson
I am doing very good, very good. And then we have David Turner with us, and you are with Turner Process Solutions, correct? Yes. I almost botched that up. Can't remember anything these days. So anyway, thank you for coming on board, David. We definitely appreciate having you here, because you're going to share with us a lot of knowledge about the world of automation and robotics, and how that's impacting the marketplace. And as you mentioned before, we jumped on here. There's been probably a number of changes since COVID, which maybe have pushed automation further now. So why don't you start by just Telling us a bit about yourself and your company, and how did you get into this industry as you are now?
[00:01:36.17] - David Turner
Okay. Well, Turner Process Solutions, we offer engineering services and automation solutions for clients. And I like to differentiate a little bit with the automation is that we got inside the pipe automation, which is valves, pumps, piping, temperature sensors, those sorts of ideas is. And then we have outside the pipe automation, which is discrete package handling, which is moving boxes from a warehousing application. But I've been in automation for about 21 years, cut my teeth right out of school with some stuff that's probably as old as I am now. And just learned with oil and gas refinement automation, went through some process safety management plants, and then through additional automation, designed some chemical feed systems for municipal water, and was most recently running the engineering Department for a global animal feed company. And now, post-COVID, started my own business, and just hitting the ground running with the automation since I've been basically training for 20 years in it.
[00:03:02.13] - Dan Paulson
Well, good for you. Congratulations on starting your own business in this. Well, let's start off with this. How has the world changed in automation since COVID?
[00:03:13.10] - David Turner
Well, there's the Technology is changing rapidly. I guess it always is changing rapidly. But a big part of what's driving it's cost, cost and availability of labor. So prior to So COVID cost was high, but labor was cheap. So the cost to automate never could quite wiggle out the opportunity for having people basically warm bodies, putting dirt in bags. So that's where that changed during COVID because one, people didn't want to be around people. You're not supposed to be. So you couldn't have a whole bunch of operators in a facility who maybe they're standing side by side on an assembly line or in their robots or in their work cell or in the warehouse. One, you had to distance people, and then two, people started getting free money, so a lot of people just left the workforce. You're getting paid not to work. I mean, it makes it really hard to say, Hey, I can give you less money, and you can put in more hours a week hurting yourself or working hard in a sweaty environment. So that really changed the dynamic. So I think automation, one, the bulk of automation didn't really lower in cost.
[00:04:54.04] - David Turner
It just got more efficient. But the change really came down to the availability of labor. No one could find people to work. So now it's like, well, robots don't need days off unless they're broken, and they will gladly work through their lunch breaks and work breaks and any other breaks that you have to accommodate for employees. Plus, they never take a vacation day. So I think from that standpoint, that That really drove the automation piece for a lot of the easy applications. The repetitive motion. Prior to COVID, it was more about economics and quality. You've got a person lifting a 50 pound box or 50 pound bag, taking the same movement, that's very bad for people. I mean, even FedEx, actually, they don't want warehouse workers longer than three years. They're actively encouraging these guys to go out and get college degrees, go out and learn a trade, and advance through their organization in a different role, because if they're doing warehousing longer than three years, then they see that injury spike. Prior to COVID, the driver was operator safety and ergonomics because back injuries are number one for warehouse workers. You get a robot to do all the heavy lifting, literally.
[00:06:43.27] - David Turner
Then that helped drive those costs. But you've got to say a $250,000 robot versus a $50,000 worker. You may be with friends, you're about $75,000 $2,000 on that worker. It takes roughly four years to pay back the salary of this person versus the robot. Most companies in warehousing, their margins are slim, and four years is a long time. That's a big part of it. Now, it's with the advent of Qobots, that $250,000 palletizer, which basically just stacks boxes on a pallet, goes from $250,000 down to $100,000 to $125,000, so about half the price.
[00:07:40.14] - Dan Paulson
What was the change that created that?
[00:07:43.26] - David Turner
It was really the change in technology. You go from industrial robots, the ones that would crush you because they don't care. With all the safeties around industrial robots, the robot moves where it's told to Regardless, it'll move there. You have safety fence, you have a whole avenue of safety that costs a lot more than a cobot safety does. The advent of cobot is a lower price, and I'm going to say, lower robust unit that can't do as much, but it can lift 50 pound boxes and put them on a pallet. With the advent the Cobot, where it's a little slower than the industrial robot, and it's slower on design, so that's safer around people. You can use area scanners to slow down the robot or even stop the robot when people come into an area where the robot could move. That lowered the cost of the implementation from about half the price. Now you're at $125,000 and a $75,000 worker a year and a half. Yeah, they'll make that leap. They'll make that investment. Plus now that $75,000 worker is maybe it's 90 because you're paying overtime, you're paying higher rates because no one wants to be there.
[00:09:20.23] - David Turner
Out in California, people working in fast food restaurants are now $20 an hour, which is roughly $40,000 a year for the base pay. So that level of skill, now, if you've got someone doing a harder job, they're going to ask for more, and rightfully so. So that sets the baseline for everyone at $20 an hour. So now everyone gets a little bit more. So now you're going to find a way to improve that cost structure.
[00:09:55.26] - Dan Paulson
And this is why I'm now ordering my own food when I go into a fast food restaurant having somebody at a cash register asking me what I want.
[00:10:03.17] - David Turner
Exactly. You're improving the cost structure through changing the work. The work doesn't change. The need to input an order doesn't change. You're just shifting it from one place to another. The work doesn't, the stack boxes on the pallet doesn't change. You're just shifting it to a different mode. And that mode is just cheaper.
[00:10:29.00] - Rich Veltre
So So it's changing the workflow. It's changing the workflow.
[00:10:34.21] - David Turner
Yes.
[00:10:36.05] - Rich Veltre
Yeah. Okay. I got you.
[00:10:38.04] - David Turner
And what it does do, though, is... So that person, say the $50,000 an hour person is worth, say, 10 pallets a day, 10 pallets in an eight-hour shift. So that's how much work he can do. That's a lot of stacking boxes. You put a robot in there, that robot maybe can do 10, maybe it can do 12. There's a higher cost structure to that robot. Now that robot they just paid, he works two shifts. Now he's worth 20 pallets. He does three shifts now. He's worth 30 pallets. That's where the cost structure changes is that investment in a one piece of machinery actually improves the cost structure the whole plant. So that's where it changes is that you're doing more is going through warehousing now because we're ordering everything through Amazon and all the other box stores that are providing shipping services because all these other stores closed during COVID. So warehousing went through the roof. And so they're trying to improve those cost structures. And with the advent of new technology, it makes it more attractive.
[00:12:09.11] - Dan Paulson
Makes sense. Go ahead, Rich.
[00:12:11.16] - Rich Veltre
From a dollars and cent standpoint, does the... I mean, Warehousing and distribution, I can see the workflow changing. Do you see that as a learning curve? Is the warehousing and distribution use of the robots the learning curve towards moving back into the actual manufacturing and not so much the distribution? Do you see the robots as... As business owners are seeing the advantages of putting the robots into the warehouse, are you seeing them also figuring out how it's going to go into the workflows for the manufacturing side, or is that so different that it's not worth mentioning?
[00:12:55.08] - David Turner
No, it's actually been in the manufacturing side a lot longer because there's more value add. When you're paying $250,000 for a robot and they're doing some intricate welding, but they're doing the same welds every day, That welder already cost you more. That person to weld was $100,000 job. It's been in manufacturing a lot longer than warehousing because margins were higher, the cost for labor was a lot higher already before even the post-COVID labor shortage. It's been in manufacturing. Now, it's just gotten cheap enough to be in warehousing for that labor pool replacement. Quite honestly, warehousing labor is a cheaper labor source than manufacturing labor because there's a different level of training and different level of awareness that's required for manufacturing. As you go through those automation pieces, it's been there. A lot of people say, Well, it's taking jobs. Well, it's actually adding higher value jobs because instead of having one person, say, three people putting boxes on pallets for eight hours a day, you've got one person that's tending robots. Well, guess what? He's a lot higher trained in technology and robot tending and programming and controls than a person stacking boxes. When you got a strong back, anyone can stack boxes.
[00:14:46.13] - David Turner
It's true. Yeah.
[00:14:50.10] - Rich Veltre
I don't personally have the strong back to be able to do it, so I'm glad I'm in an office. Yeah, I was curious about that because I think the other thing that we think we see, obviously, a lot of this is where we think it's going. And I think that manufacturing is coming back. I believe it's coming back in the areas that we haven't had in a long time. And the immediate question everybody says is, well, who's going to do the work? Because we have the same problem, it's just manufacturing has to come back here. Covid was the teacher. Too much stuff was overseas, too much stuff sitting on ships that couldn't get into the United States. So all of a sudden, everybody's saying, we have all these shortages. So there's a big push, I think, for people to figure out how to push manufacturing back into the US. And from what I'm hearing, and see if you can confirm or if you think I'm right, I think automation might actually be the... What's the word? Impetus, the push to have that actually happen. So that's the way I'm thinking. What do you think?
[00:16:14.14] - David Turner
Absolutely. Yes. All plants are being... All new plants are being automated heavily, state of the art. There's very few facilities that are being built that don't have a certain level of automation just because of, one, the skill shortage, but two, just general cost improvement quality. Because a machine is going to turn a valve. It's going to adjust the temperature. It's going to move product at the same rate every time, day day in, day out. You're going to improve your quality. You're going to improve your cost structure because a machine doesn't fall asleep. A machine doesn't get distracted. A machine doesn't There's no human error involved unless... And don't get me wrong, because machines are only as smart as the person that programmed them. So machines can royally screw up, too. But it's the programmer's fault because Because they didn't think through all the processes. I've seen some terrible stuff happen, but it was ultimately, if a machine screws up, it's on the controls engineer because they didn't think through all the processes. Regardless of what happened, if someone closes a valve, they should not have either... The machine should know it's closed or they should not have been able to close it while the machine is running.
[00:17:56.26] - David Turner
Because if that happens, some Something else should happen to compensate, whether it's shut down or whatever it is. So there have been terrible incidents involved with automation, but it comes back to If a person is allowed to make a mistake, then it's the control engineer's fault because they should not be allowed to make a mistake. Now, there are incidences around where people do it on purpose, but that's typically their stuff's getting broken. Forklift runs into a valve head and it breaks off, stuff like that. But for the most part, people want to go to work and they want to do a good job. We need to give them the tools to go to work and do a good job and go home every day. No one wants to go to work and be yelled at or not do a good job. I mean, everyone who's working to do a good job. And so we're just trying to give them the best tools in the system to be successful. And if they can't be successful with the tools we give them, then that's on us.
[00:19:15.17] - Dan Paulson
Now, how does that change? And this isn't to go political, at least not to the degree of what we typically see in the world today. But we have a lot of people coming into the country by various means. The The argument has been made by certain politicians as well, we need these people to do jobs because we have people in the US who don't want to do those jobs. According to what you're saying, if we're automating a lot of these, we consider more repetitive entry-level type positions, Isn't that changing the dynamic? Are these people going to have any jobs to work at? Now we can make the argument and say, well, technically they shouldn't be working anyway because they don't have the documentation to do so. But I think most people in the real world know that somehow those people do manage to find ways work. So are we creating a bigger problem for ourselves with that?
[00:20:07.04] - David Turner
I would say no. And the reason I would say no is because it's just another way to improve the cost structure. I mean, if someone is touting for immigration to take on low paying slave labor and bring in people, then they're already on the wrong side of the fence. We want good high paying jobs. That's technicians, engineers, maintenance personnel to take on automation, trained operators. Yeah, absolutely. And you invest the capital into automation to have these higher level jobs doing more value add processes. Because go back to the $200,000, $250,000 robot is competing against a $75,000 labor pool. Well, now a $250,000 robot is competing against a $20,000 labor pool. So all you've done is you've suppressed wages by increasing increasing labor access to lower paying jobs. So it's not good for anyone because you're changing the dynamic by flooding the market with people who are willing to work for less when ultimately you should be focused on having jobs for everyone that are more value add to a company. A company can only pay as much as its product is worth. That's it. Right. And so if you have that process of labor where you can either pay a little for unskilled labor and it does a job, or you can pay more for skilled labor and have your capital automation investment, and you've improved your cost structure.
[00:22:29.12] - David Turner
Those are just ways to improve cost structure of your product. Now, I'll argue that one has a higher quality because there's less human error involved. I've made my share of mistakes in programming, and I made my share of mistakes in putting dirt in a bag. I mean, I'm only human. I'll make a mistake every now and again. You've got to make a process that is mistake free. And unfortunately, having SOP operating procedures written on paper and expecting someone to follow it every time just leads to quality and process errors. So to me, automation, the machine, as long as it's done right, a machine is not going to make a mistake because it does it the same way every time. Its mistakes are based on its programming.
[00:23:28.16] - Dan Paulson
Yep. So that leads to a different question, I guess, along the same line. So you've mentioned the cost of some of these robots and some of this automation has come down drastically, especially in the last couple of years. At what point will a, I'll say, a smaller manufacturing firm be able to justify the cost of the automation over the cost of the labor? Because I live here in the Midwest. So we're not in New York City. We're not in a large industrial town. And there are several, I would say, small to medium-sized manufacturer is probably making anywhere between 5 million to 50 million a year. Where does it justify to turn that over to an automated process versus having another body come in there and do the work?
[00:24:13.25] - David Turner
It really depends. It depends on what they're doing. It depends on growth. So the small to medium businesses are actually where I focus, where my company focuses, because we're looking for one of two things. We're looking for zero automation because we can provide value to zero automation at a lower price point. We're looking for more repetitive tasks that can be automated easily. Because if you're, say, you're tearing apart a motor, a motor is a complicated piece of equipment. You're not going to automate that easily. It's going to be very cost effective, high engineering involvement. So like motor shops, auto repair places, not a focus. That's too intricate a task. Filling bags with with sunflowers seeds. I follow a smacking sunflowers. It's a new company that's enough to come around, and they're super, super awesome growing, and I've just followed them. But they recently showed a form, fill and seal bag packer. Fantastic. They're growing. So now instead of having someone with a scoop and just scooping stuff into a bag, you buy a machine because now growth has demanded that you work faster. It's a crux with the small to medium where, one, either you can't find labor and you're you're growing, or two, you're growing, you can't compete with the big boys because your cost structure is wrong.
[00:26:11.15] - David Turner
It's too labor-intensive. We look at those opportunities, and some of it's just some of its sheer quality, like a stamping machine. A stamping machine rolls out flat steel and cuts it at a length.
[00:26:29.16] - Dan Paulson
Right.
[00:26:30.05] - David Turner
Continuously. You're relying on some Timer or some measuring device. Maybe it's a person to cut it to length every time. Well, what's the tolerance on that? How can we improve that quality of that product so you can have less waste? It really comes down to how does those small to medium businesses see their need? Is it reducing waste? Is it improving output? From sheer growth? Is it a labor shortage, especially in smaller rural areas where you don't have enough people to run a third shift? Say you've got so many people in the area and you've got more orders now. Everyone's on the internet. You're starting to sell on the internet. Maybe you're shipping more now. Maybe you've got to package your product differently. Instead of putting it on the... Putting it in the back of your truck, now you've got to actually palletize it to get it on an LTL freight. Well, there's an opportunity. It's a growth opportunity. It's great. People are growing. You've got to make an investment knowing that you're going to be there a little bit longer. And with Qobots being so relatively cheap now, you can find Qobuz palletizers, depending on...
[00:27:58.01] - David Turner
Just out of the box now, less than $100,000. They deployed on your site less than $100,000, and it'll package, it'll palletize 50 pound boxes. Three shifts a week, three shifts a day. I mean, it's just continuous. So you can't beat that with adding headcount.
[00:28:24.10] - Dan Paulson
Now, how about something that's probably a little bit more, we talked about welding and stuff like I can think of a client, for example, make screens and racks and maybe 100,000 of them at a time. Well, he has a small robot there, but he still has a lot of labor in place to do that. He'll tell you it's very difficult to get that labor and get it skilled enough to where it can do the job. At what point is there a shift where he should really be looking at maybe doing more automation instead of worrying about where he's going to find the next welder?
[00:28:59.17] - David Turner
Today, Yesterday.
[00:29:01.04] - Dan Paulson
Well, maybe he'll listen to this on Thursday.
[00:29:05.05] - David Turner
I mean, if you're already struggling with labor, you've got to look at your process. I mean, is there a way to get more out of your process? And the answer is always going to be yes, always. So then you define, here's the process flow, where Where's my bottleneck? Does the person have to walk back and forth to the stock room constantly? There's wasted time. You can get rid of that. Bring all the stock to him on the floor or move the work cell closer to the stock room. Items like that are low quick wins to get you an incremental piece of productivity improvement. Going a step further is, Okay, well, I've got one welder and he's fantastic. I need him to weld all my high-quality stuff. And then I got some other guy who just got out of welding school. He's a little green. He can weld all the handrails. No big deal. He'll weld them, he'll grind them down, they'll be fine. Not great, not piping, but good enough. Well, there's If you can't find that next guy, or maybe he's slow, or you sold out your handrails, and now he's got to do it again, he's got to get a second shift, then you've got to look at, well, is there another guy out there?
[00:30:43.15] - David Turner
Or can we train him up to do the other job? Or can he train somebody? From that standpoint, you're already struggling because now you're full. You've got to look. Anything you do is going to set you back, period. Because training takes time away from the actual job. So around 50 to 80% capacity is when you need to start looking at your next step. Because if you're more than 80% capacity on your product line, then you can't grow. You absolutely cannot grow. That last 20% is just a buffer for a quick order, really. I mean, That allows you to be flexible enough to take on a new client who comes to you saying, Well, I've never worked with you before, but I have an immediate need. Let me give it to you because you say you can do it. That helps you get your foot in the door with new clients. Once you're 80%, you got to start looking. You got to be improving your capacity. Whether it's through improvements in the current system or whether it's through automation or buying a new system, you've got to make that decision. If you're already struggling, you're already behind.
[00:32:11.05] - David Turner
To me, I I sell a welding robot. I rep a welding robot that's $65,000. So it's the same price as a welder. And a welder operates it. It's designed for a welder to operate. Because once he sets up the program, he pushes go, and it'll run the program, and he can go set up the next one, or he can go grab the supplies for whatever task is next. So it's that kick around where it's able to... It's user friendly, it's cost effective, and it's deployable in a day. So now you can cut the check, get it on site, and be off the ground running in less than a day. And so the next day- So what's the learning here for the welder to actually pick it up for the programming side of it?
[00:33:13.13] - Dan Paulson
Is that something that's pretty intuitive Or is that where the learning curve is going to be?
[00:33:19.20] - David Turner
It's very intuitive. I mean, you've got some robots, the industrial welding robots. A welder is never going to... It's not never going to learn, but it's a lot... It's weeks. Weeks and weeks of training. Cobot welders are more point and click, really. You move the head to the start, you orient it the right way, and you click a button. Then you move it to the end of the line, you reorient it, and you click a button, and you push go. Like 10 minutes, you can have straight line welding. Curves take a little bit more time, but they're still doable. So the learning curve is roughly 2 to 4 hours. Okay. And as long as your fixtures are right, then it'll... Again, a robot is only... A robot is going to do exactly what you tell it to do.
[00:34:11.08] - Dan Paulson
Right. It'll do it- Good, bad, or otherwise.
[00:34:14.23] - David Turner
Good, bad, or otherwise. So I think now with the way the way co-bots are coming and improving the safety around articulated arm movements and We're improving the price. I think we're really getting to a point where the trade shortage that we have today that we'll have in 10 years where half a million tradesmen are going to be retired, you're not going to have welders and plumbers. Plumbers, completely different because that's a different task altogether. But welders, I mean, kit welding is fairly repetitive. I think that from that standpoint, it's fairly easy. A lot easier to automate.
[00:35:01.14] - Dan Paulson
Well, since you brought up the trade, since you went there, how is it going to change the trades? Because I work with construction companies, and the challenge of finding plumbers, electricians. We won't even get into the welder side of things. But you have a number of trades people that, whether it's putting up a wall or running conduit, how is robotics and automation going to change that industry?
[00:35:29.11] - David Turner
You're going to You're going to have to have a more versatile skillset to be in the trades. I've seen it. I've seen videos. I haven't seen any construction robots in person, where robots laying drywall or laying floor or painting walls. I haven't seen those in person. I'm only on videos. They look pretty cool, but There's going to be a cost to it. And that cost has to come down drastically because right now, they're still expensive. But I think a long term, you'll have tradesmen who know what to do, but they need to tell a three-year-old how to do it. Because basically, that's what you're doing when you're automating is you've got to know your process so well that you can tell a three-year-old how to do Because a three-year-old will do exactly what you tell them to do. It's good, bad, or different. So that's the same thing with automation. It's only as good as the person who programmed it. Sure. I think from that standpoint, honestly, it may entice more people to trades because it'll be more game-like, and I've seen people talk about gamification of the trades where people are... You're setting up a program and letting it run versus sweltering heat outside, nailing up walls or running wire or running conduit and a 110 degree wet end of a paper mill.
[00:37:26.27] - David Turner
I think it'll They've definitely improve the productivity of trades, but the skill set's got to change. They got to know two things. They got to know programming, and we're working that. Automation is coming down, and then they also got to know their actual trade.
[00:37:43.22] - Dan Paulson
Yeah. Well, I know a lot of the challenge in the trade industry is you're pointing out the guy putting boxes on a pallet and how FedEx doesn't want them doing that more than three years. Trades is really no different. I mean, it's a very physical task in most cases. And these guys, for example, my daughter's boyfriend is in the trades and he's an electrician, and he's already thinking ahead saying, well, if I do this for another 10 years, my body is going to be shot. So I have to advance my career into either doing my own company and then hiring other people or then moving into a management role where I'm doing less of the the actual physical work and I'm managing other people. And I'd almost guess that we're in the same situation here where if you can put that automation in, you're going to allow that employee to last longer and less work on their body or less damage to their body as they're doing these jobs. Because if anyone's done construction, it's not easy by any stretch. It's very physical labor. And these guys do get burned out pretty quickly. I mean, there aren't too many construction people past their 50s that aren't in constant ache, pains or have all sorts of other physical issues going on.
[00:38:59.01] - David Turner
Oh, absolutely. I I think it'll definitely extend the life of a construction worker, the useful life. I mean, otherwise, it is backbreaking. I mean, you're carrying shingles onto a roof, especially in the middle of summer.
[00:39:16.25] - Dan Paulson
It sucks. That's when you like doing roofs.
[00:39:21.21] - David Turner
So I think from that standpoint, I think you're just going to have to be more versatile. You're going to have to learn more And with more knowledge comes more value and more value means you charge more. So I think that we may have less jobs, but they're higher value jobs. So you're not making $30 an hour running conduit. You're making $40 an hour telling someone, some other machine how to run conduit.
[00:39:59.10] - Dan Paulson
Well, that match where our population is going anyway. We have fewer people as far as our population growth. So that would only make sense that the more we automate, it does push you into higher value jobs, which ultimately should help everybody.
[00:40:13.08] - David Turner
Absolutely. Absolutely. I It just makes sense. I mean, you want to improve your life as much as possible. Work-wise, you don't want to be in a non-air-conditioned office, nice and cool, and you want to save your body as much as possible. Why do back-breaking work? And quite honestly, that's where a lot of people find themselves is they're literally ruining their quality of life because of the jobs they're doing. And it comes down to maybe they get paid a lot for what they do But they're paying for it in the long run. Yeah. Right.
[00:41:05.11] - Rich Veltre
Absolutely right.
[00:41:09.04] - Dan Paulson
Rich, you got anything to add to that? Where's your finance questions? Come on here. So much to process. These things are expensive.
[00:41:15.24] - Rich Veltre
So much to process. No, I think we've hit those points already, right? I think, yes, there's a cost to the investment of getting the the material or the machine in place. And I think in the past, the cost was higher and the resistance was higher. Nobody wants to lay out $125,000 on a machine But now you're starting to see why, which you didn't see before. Now you're starting to see it because of the labor change, because of people are being forced to actually relook at it. And the people who build the manufacturing the ring pizzas or the robots have recognized this as an issue and found a way to get the cost down. So the finance questions are pretty straightforward. I mean, it's essentially people are starting to look at it now and say, this solves my problem. I just have a different problem, and I have to find $125,000, or I have to find the way to put that in. And I think the biggest piece of it that I'm taking away from it is we may just be in a flux, right? Because those two things have started to happen, but they haven't met in the middle yet.
[00:42:32.27] - Rich Veltre
And I think, and somebody's going to tell me I said that wrong, but that's okay.
[00:42:38.11] - David Turner
I wasn't. I don't think they've met in the middle yet.
[00:42:43.01] - Rich Veltre
And I think when they do, it's going to become much more prevalent. I think we won't be having these conversations. It'll be different conversations because this one will already have been settled, that business owners who are in those markets that can use, as David said, repetitive machines that just do it over and over again. I think that those two pieces will meet, and then we'll be off to the next problem. Because the question is, is it really a problem or is it really solved? And people just have to realize that it's solved.
[00:43:15.00] - Dan Paulson
Well, the next problem is going to be the programming. True. But we're not going to have enough people programming the robots to do their jobs is what I see happening, especially just based on what you're saying, David, because I have family in the trades. Again, I work with a number of contractors that they look for different ways to automate. But I'd say it's more very basic automation that's happening right now. And I know these kids coming up through the apprenticeship programs and whatnot. Automation is talked about, but not really talked about. If you get by drift, they might bring it up, but they're like, that's too far away. You don't need to worry about programming now. And really, based on what you're saying, the kids now should be starting to get into this, at least get an understanding of what's coming so that they're prepared.
[00:44:02.11] - David Turner
Yes, absolutely. They need to understand what's coming. I mean, my kids are 12 and 15, and I'm teaching them. I've got my daughter doing AutoCAD Nice. Because she wanted to learn how to make GFXs, which is a graphics data file for Roblox. So she was literally when she was 13, she was doing GFXs for Roblox and trying to sell them through Discord.
[00:44:36.28] - Dan Paulson
I like the entrepreneurial spirit there.
[00:44:41.11] - David Turner
I know. I loved it. And so I was like, okay, well, AutoCAD is very similar to the software she was using to make the graphics. So we just migrate over and learn something new. And it's just a different tool. All the knowledge is in your head just using a different tool to put it down on the screen. So But I think from a programming standpoint, people need to know coming out of school what's coming down the pipe. But programs are changing. They're getting less and less proprietary and more and more intuitive, where it's basically dragging and dropping boxes on the screens for go, no, go functions, something super simple. It's if then if then statements. So very, very rudimentary programming opportunities because the behind the scenes, the engineering side of it is already being done so that now the user interface side of it is very intuitive. It used to be there was very little user interface, and so you had to dig into the background of the program and you're doing structured text and ladder logic because that's just what was available to you. But now it's changed so much that it's almost graphical.
[00:46:09.11] - David Turner
I mean, there's programs out there now where it's literally You're dragging boxes on a screen and connecting them with arrows. And it's node reds one key one where it's super easy. It's just a different level. It's the same level of thinking. It's just a different way to put on the screen.
[00:46:31.29] - Dan Paulson
Right. So how will AI change all this? Is this just another added benefit that we could see from AI? Where we'll start doing the programming for you?
[00:46:45.04] - David Turner
Only if it's been done before. Ai is just a faster way to regurgitate someone else's ideas. That's true. That's all it's doing. It's nothing novel. It's just regurgitating what someone else has done. It just finds it faster and is able to put it together faster. So from a novel programming standpoint, no, not yet. But if it's been done before, then, yeah, I think it'll help. It'll help the plug and chug of programming get through, I think.
[00:47:24.25] - Dan Paulson
So it might become an auditing tool in the future, especially for maybe a company that It's got a lot of automation, where you might be able to pull in that automation, say, okay, now we're doing this, how do we change it, or how do we make it more efficient? Ai may be able to help with that at some point in the future.
[00:47:41.29] - David Turner
Yeah, I could see that. I don't know about improving the efficiency I can see because that's still a novel task, but maybe it can help with identifying bottlenecks for sure.
[00:47:51.20] - Dan Paulson
There you go.
[00:47:53.06] - David Turner
Okay. Yeah, you can run the AI tool. It'll tell you exactly where bottlenecks are.
[00:47:59.08] - Dan Paulson
Interesting. Well, we'll see how all this goes. So that leads to the title of this podcast, Our Robot is going to Rule the World. You give me the pitch on that one. So do we need to be worried about the Terminator anytime soon? Or is it the Turnernator?
[00:48:17.20] - David Turner
The Turnerator. No. Again, AI is not taking over the world, and robots are only smart as a person that program them. So if a robot's eyes turn red, those eyes were put, they were put in there by somebody. So there was already a program in place to make their eyes turn red. It wasn't anything random. So again, they're only doing what they're told. So if they come after us, someone told them to.
[00:48:51.05] - Dan Paulson
All right. So we're safe from Skynet at least for the next couple of years.
[00:48:55.13] - David Turner
At least in the next decade. Right.
[00:48:59.25] - Dan Paulson
Well, David, thank you for participating in this. This has been great. How do they get a hold of you? If somebody's curious about automation and robotics.
[00:49:09.07] - David Turner
Turner Process Solutions. We're on LinkedIn. My website is turnerprocess.com. Send me an email at david@turnerprocess.com or solutions@turnerprocess.com.
[00:49:23.21] - Dan Paulson
Excellent. Well, good. We will definitely get that out there. Rich, how about you? How do they get a hold of you if they need to figure out how to finance these damn robots and get them into place.
[00:49:33.04] - Rich Veltre
E-mail is always the best at rveltre@veltregroup.com.
[00:49:37.04] - Dan Paulson
And for all the other processes that can't be automated dealing with culture and people, you can get a hold of me at danpaulsonletsgo.com. That's the website. And there is a form there you can fill out, set up a meeting, we can talk further. David, thanks again for participating. This has been fun, and we will have to check back in with you the next time we have some automated questions come up, or maybe there's a new process that pops up that takes over the world, and we can talk about Skynet then, and see if you were right on your predictions.
[00:50:07.07] - David Turner
7:15, 20:34.
[00:50:09.15] - Dan Paulson
There we go. All right. Sounds good. We'll mark it. All right. Thanks again, everybody. We will talk to you next time. All right.
[00:50:15.20] - Rich Veltre
Thank you.